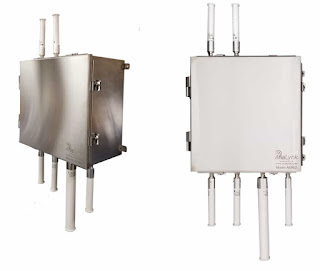 |
Analynk AE-902 ATEX Zone 2 and Class 1,
Division 2 Groups A, B, C & D Enclosure
with ISA100a/WirelessHART Gateway and
Aruba AP-318 Access Point |
Deterministic behavior has long been a requirement for critical control networks in potentially explosive environments, and industrial customers have relied on ATEX Zone 2 or Class 1 Division 2 WirelessHART or ISA100a for years to monitor flow, pressure, temperature, and other wireless sensors. These rudimentary control standards lack advanced cybersecurity features but are very high-speed and low power, making them attractive to oil and gas customers in particular.
Customers are often confused about the pros and cons of purchasing an access point with an integrated 2.4GHz WirelessHART or ISA100a sensor network transceiver, or purchasing a separate control gateway and access point. One of the issues with an integrated access point is that the ideal location for a sensor network antenna can be very different than for a Wi-Fi antenna. The former needs to be within line-of-site of the sensor mesh, while the latter needs to be in line-of-site of roaming client devices and potentially other backhaul access points.
A second reason for remotely locating the sensor network antenna is to avoid interference between the 2.4GHz WirelessHART or ISA100A sensor network and the 2.4GHz Wi-Fi network. WirelessHART uses 2.4GHz 802.15.4-2006 (ZigBee) radios with a channel hopping mesh and time- synchronized messaging. ISA100a also has a single physical layer using 2.4GHz 802.15.4-2006 radios with listen-before-talk operation, short messages, low duty cycle, and adaptive frequency hopping. While both control networks are intended to operate near other wireless network, the reality is that the RF signal degrades with in-band interference, and also interferes with 2.4GHz Wi-Fi channels. Frequency planning, antenna location, and antenna separation must all be considered during the design and implementation phases.
Typically the sensor and Wi-Fi network antennas must be separated by at least one meter, potentially more depending on the frequency of sensor transmissions and the power output and antenna propagation pattern of the Wi-Fi access point. By definition that means one of the systems will require an external antenna and lead-in cable.
Another reason for separating the sensor gateway and Wi-Fi access point was touched on earlier: Wi-Fi is changing at a very fast clip whereas WirelessHART and ISA100a are not. Staying current with technological changes in Wi-Fi requires more frequent updates than do sensor networks, for which change has been very slow. That calculus may start changing after 2021 by which time the new 802.11ax standard could start displacing WirelessHART and ISA100a, leading to hybrid deployments in which new 802.11ax devices have to coexist with WirelessHART and ISA100a. Until that time, separating the sensor gateway from the access point allows RF performance to be optimized for each system while minimizing the impact of RF technology transitions to existing infrastructure.
Technology suppliers have recognized the benefits of building separate sensor gateways for use in potentially explosive environments, and there are multiple vendors for these devices. For example, ArubaEdge technology partners build ATEX Zone 2, Class 1 Division 2 gateways for WirelessHART and ISA100a control networks. These gateways can be connected to a nearby Aruba switch or access point using an Ethernet interface cable up to 100 meters in length, longer if a fiber optics adapter and cable is used. Gateways with a built-in antenna and don’t require a remote antenna or lead-in cable.
If the sensor gateway and Aruba access point must be co-located for cost, convenience, or antenna positioning, an ArubaEdge partner gateway circuit card can be installed in the same explosion-proof housing as the Aruba access point. That design requires an external sensor network antenna and lead-in cable, however, it allows the Wi-Fi access point to be updated as needed without needlessly replacing the sensor gateway.
To learn more, read the entire white paper from Aruba Networks. You can
download it from the Analynk website here.