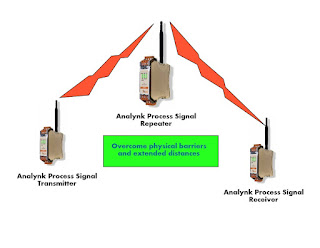 |
Wireless connections for industrial process signals |
The operating personnel at almost every facility have something to which they would like to connect. Remotely located equipment, activities that require a human to be present to monitor operation, and other scenarios are all candidates for a wireless connection. Have you ever thought that it would be helpful to know more about the current status of a remotely located piece of gear, for example, the
back-up generator located across the parking lot? Budgets, time constraints, cabling difficulties, and other factors seem to continually outweigh the benefits of making the connection and gathering the data. Those days are gone. In fact, they have been gone for some time.
Industrial wireless transmitters, receivers, and repeaters can be applied in place of wires, cables, conduit, trenches, overhead supports, and all the other hardware associated with a wired installation. Data is gathered using whatever process measurement hardware you prefer, just specify commonly used output signals like 4-20 mA, or a host of others. Connect the measuring device output to the transmitter input. Locate a receiver where you want the sensor information delivered. The transmitter converts the sensor analog signal to digital and the receiver converts back to analog. The connection can be accomplished in a very short amount of time without disturbance to the real estate between the two points.
How can I tell if the wireless connection can be accomplished without interference?
The transmission is accomplished in either the
900 MHz or 2.4 GHz band, delivering adequate range and power for most facility-wide applications. Obstructions can be overcome with the use of a strategically located
repeater.
What about power needed to operate the sensors and wireless equipment?
Most process sensors have very small power requirements, as do the Analynk transmission units. Power, if line voltage is not available at the location, can be provided by batteries, or combination of battery and photovoltaic. Little power needs to be provided for operation.
There may be simple and effective wireless solutions to many of your remote monitoring challenges. Don't assume it is difficult, it is not. Don't assume it is expensive, it is not. Share your ideas and challenges with the experts at
Analynk. Combining your facility and process knowledge with their technology and product expertise will lead to effective solutions.